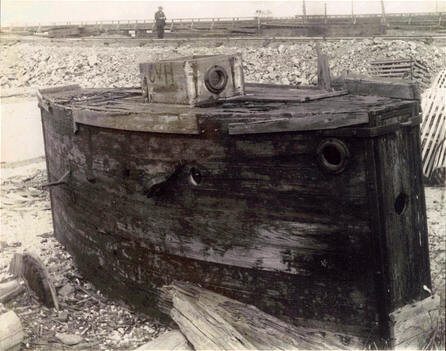
We wheeled the Argonaut Junior to the water’s edge and launched her very informally. No one broke anything over her bow. Her pine sides were so frail that a hearty swing with a bottle might have cracked them, anyhow, and I knew that with her construction of flat surfaces she could stand little pressure. But I did not propose to strain her. — Simon Lake
She had a double skin of yellow pine, with canvas between the skins, and was well calked and payed. –Simon Lake
The original Argonaut Jr. was two layers of yellow pine boards, with a layer of canvas and tar between them to make it waterproof. It fasteners were mainly nails with some bolts. “Payed” is a messy process of ramming cotton and tar into the joints between the boards.
Argonaut Jr. 2010 used laminated sheets of plywood and solid wood beam framing, held together with epoxy, fiberglass tape, screws and construction adhesive. Only the screws and wood beams were available when Simon built Argonaut. We think he would be impressed with the advances of the past 116 years.
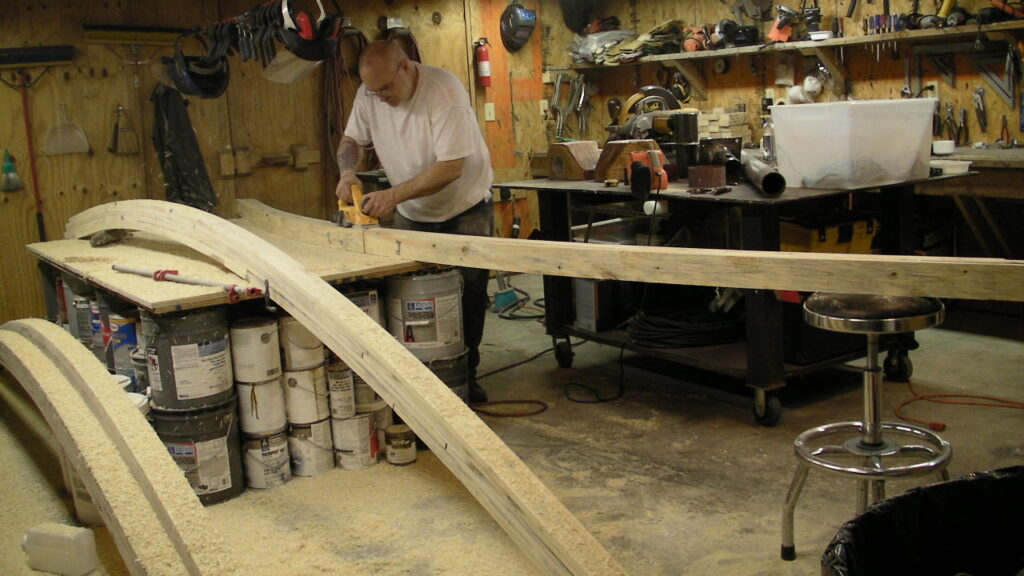
Plywood protected from the water with sealant and paint is the logical choice for the hull material. Normal exterior grade 3/4 inch 4×8 foot sheet plywood from the local lumber yard is about $20 a sheet, but it will likely have voids inside and the wood used to make the layers or plies will have knots so it is not as strong as marine plywood available local contractor lumber suppliers like M & M for $75 a sheet.
Testing Plywood and Construction Adhesive
Marine grade plywood is often use for boats because is is constructed from more plies than regular ply wood and more care is take to make sure there are not voids in the ply that would cause a weak spot. We wanted to make sure we were getting our money worth, especially considering that marine plywood is almost three times the cost of regularly plywood, and we waned to know how much damage might be done by letting the boat sit in the water for almost two months. Lowes gave us a sample of their regular plywood and we purchased a sheet of marine plywood from M & M.
In addition to the plywood the glue used to hold parts together was very important. We wanted to limit the number of screws used because a screw hole provides a path for water to enter and weaken the wood.
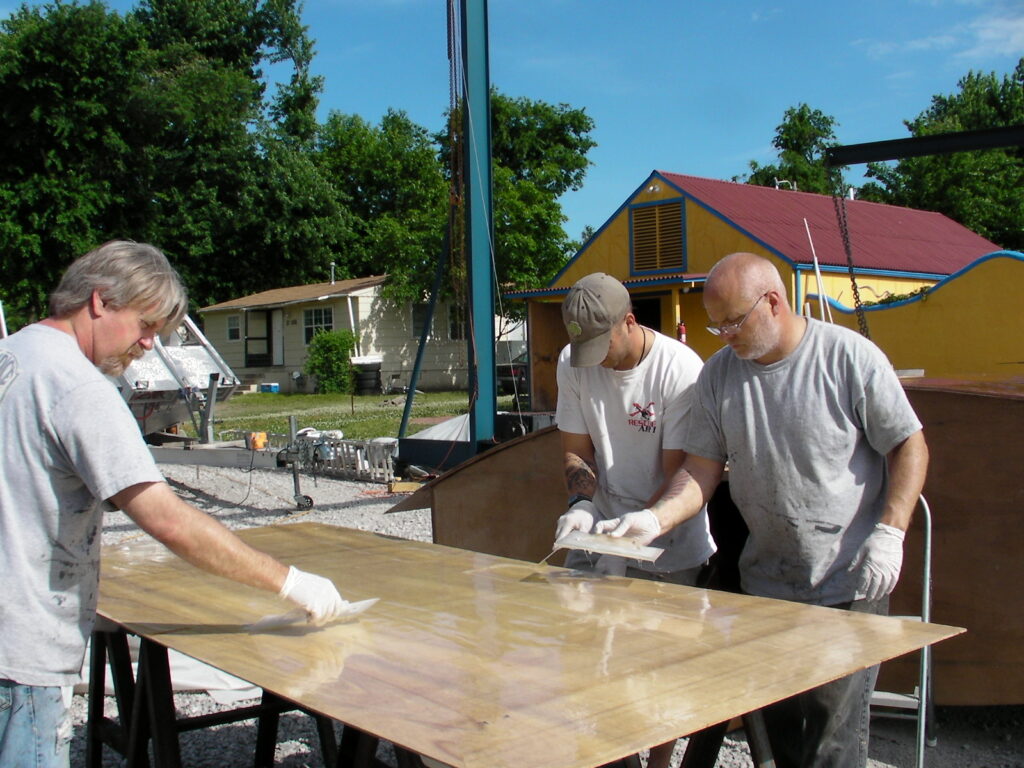
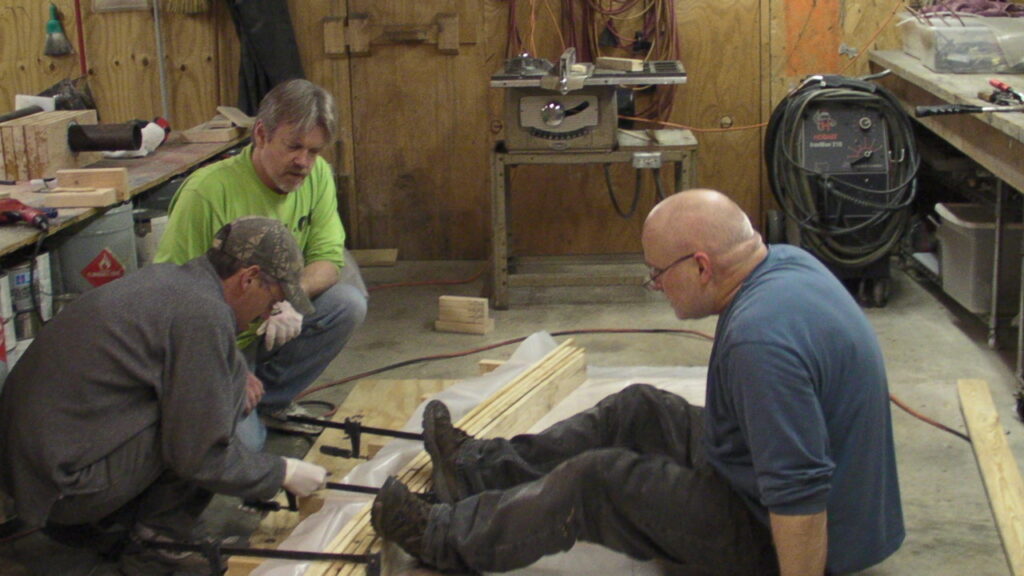
Joining Plywood Panels
You can join plywood panels in a number of ways if you need sizes greater than standard ones. Scarf joints are the best approach for strength and weight. (If you order 16′ long panels, offered by some plywood suppliers, the panels are simply scarfed together, but you will pay a premium both for the material and the shipping.) Gougeon Brothers, Inc. does offer a custom attachment (875 Scarffer) that fits onto a circular saw. This tool makes scarfing plywood panels of 3/8″ thickness or less quick and accurate. You can also fashion scarfs with a plane and/or grinder. The rule is to create a bevel 8 times the thickness of the plywood. Panels can also be joined with butt blocks, but this has the potential for exposing end grain at the butt. We like to dish out the butted area similar to a scarf and bond in fiberglass cloth.”
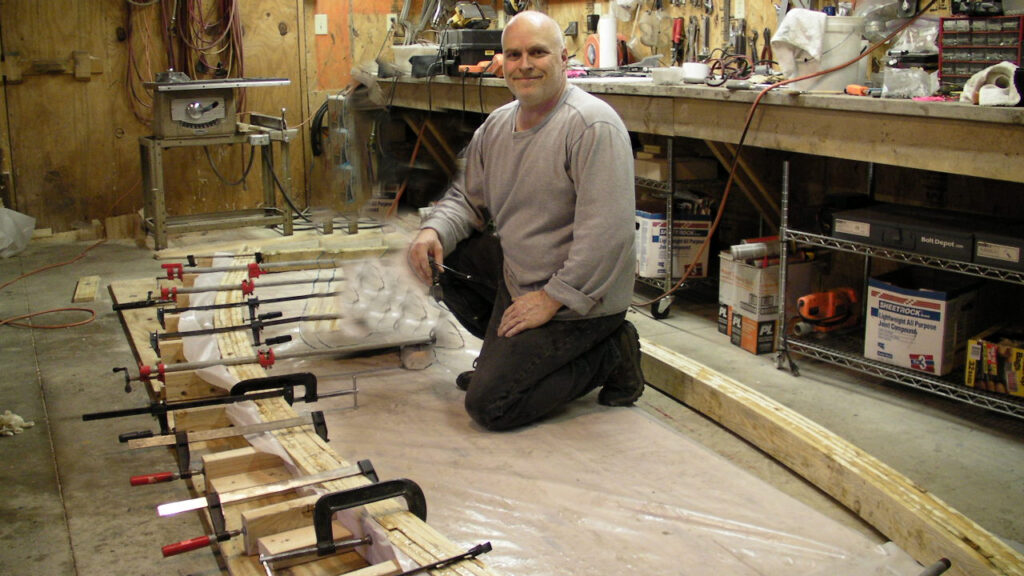
Laminating Plywood and Curved Beams
Curved beams make up the top and bottom frames. In 1894, Simon might have cut these from solid wood, or even taken them from a old ship. Today curved beams are often smaller boards which are glued, bent to fit into a form with the desired shape and clamped in place until the glue cures. Afterwards the clamps are removed and the glue holds the boards together and in the correct shape. That is how we will build the top and bottom beams for Argonaut Jr. 2010. The each of the two curved bottom beams is build from 5, 1 x 4 board so it will be over 3 3/4″ wide. The top beam is build from 6, 1 x 4s making it over 3 1/2″ wide. Another advantage to laminating beams is that we can save time and money . These beams are about 14 1/2 feet long but we can buy less expensive 8 foot boards and simply butt joint the boards together to make the full length. The trick is to simply not put two butt joints in the same place on the beam.
The same laminating process can also be done for the plywood. A single 1 inch thick sheet of plywood can be laminated from 4, 1/4 inch sheets. This will be especially helpful on the large curved sides of the hull where bending a 3/4 inch thick sheet of plywood would be difficult and add considerable stress to the hull. Laminating also avoids the need to scarf the joints between the sheets of plywood because each joint will be offset from the others and supported by the other layers. We also get the advantage of better water proofing. The outer layer of plywood can be damaged and allowing water to seep into it’s layers and weaken it, but the epoxy glue between that layer and the next will prevent the water from reaching the second layer.
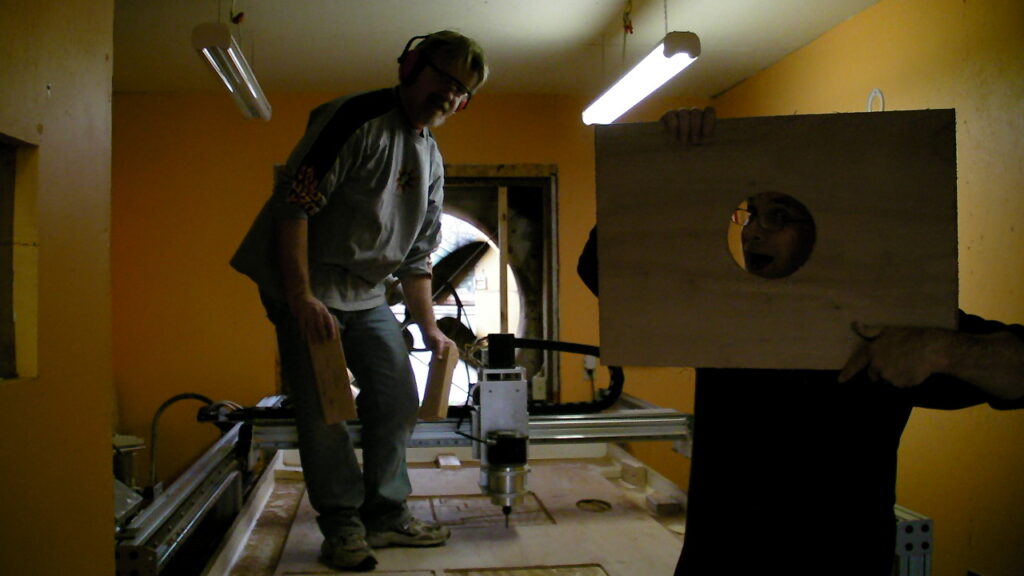
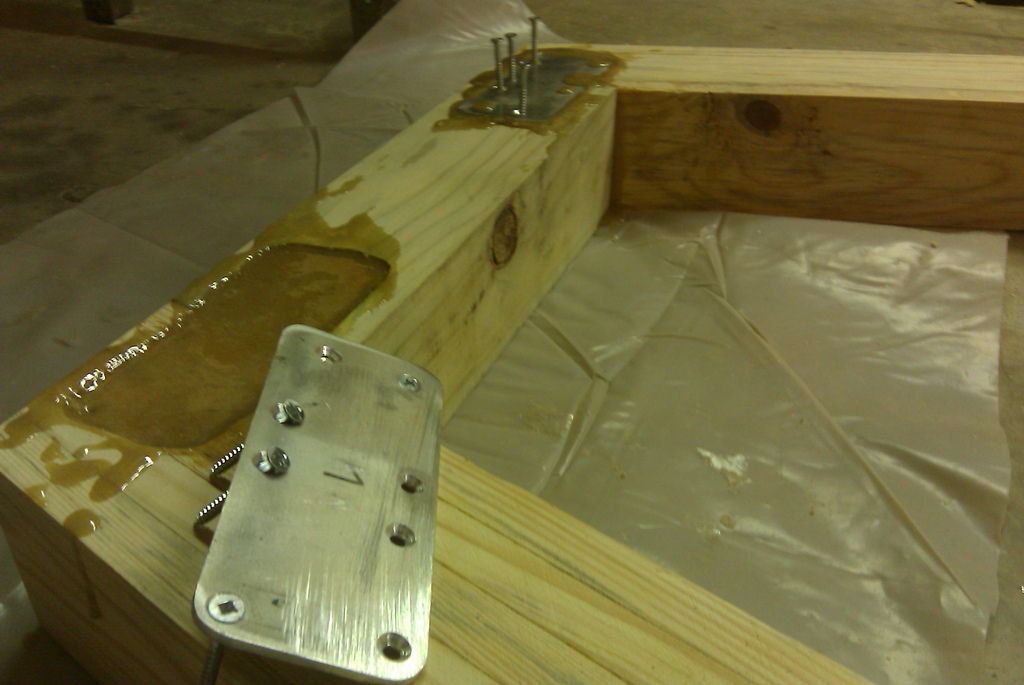
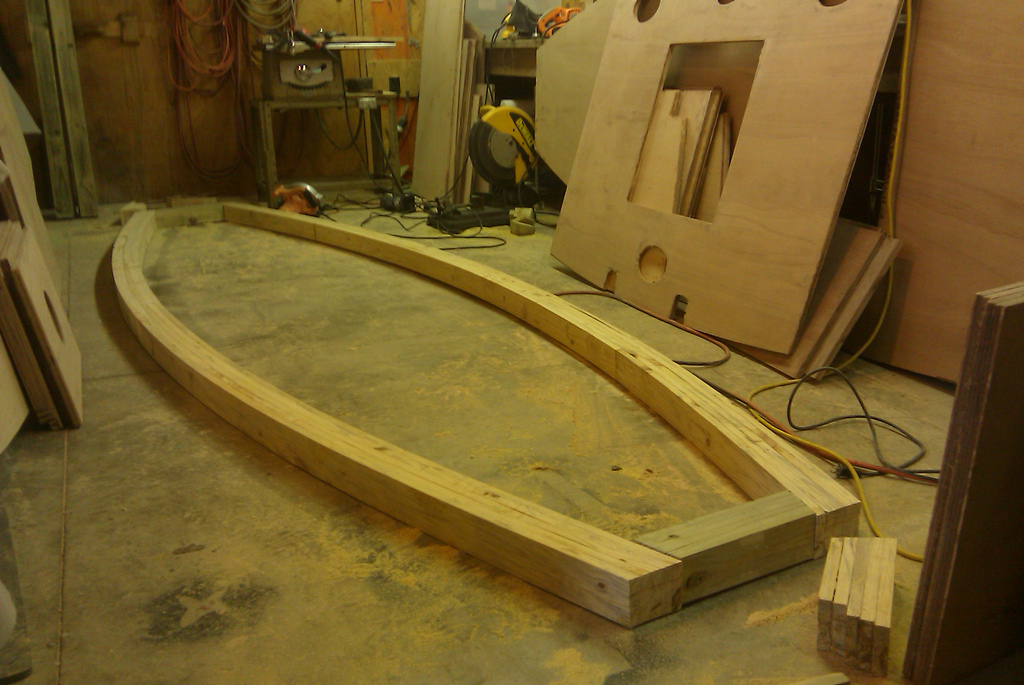
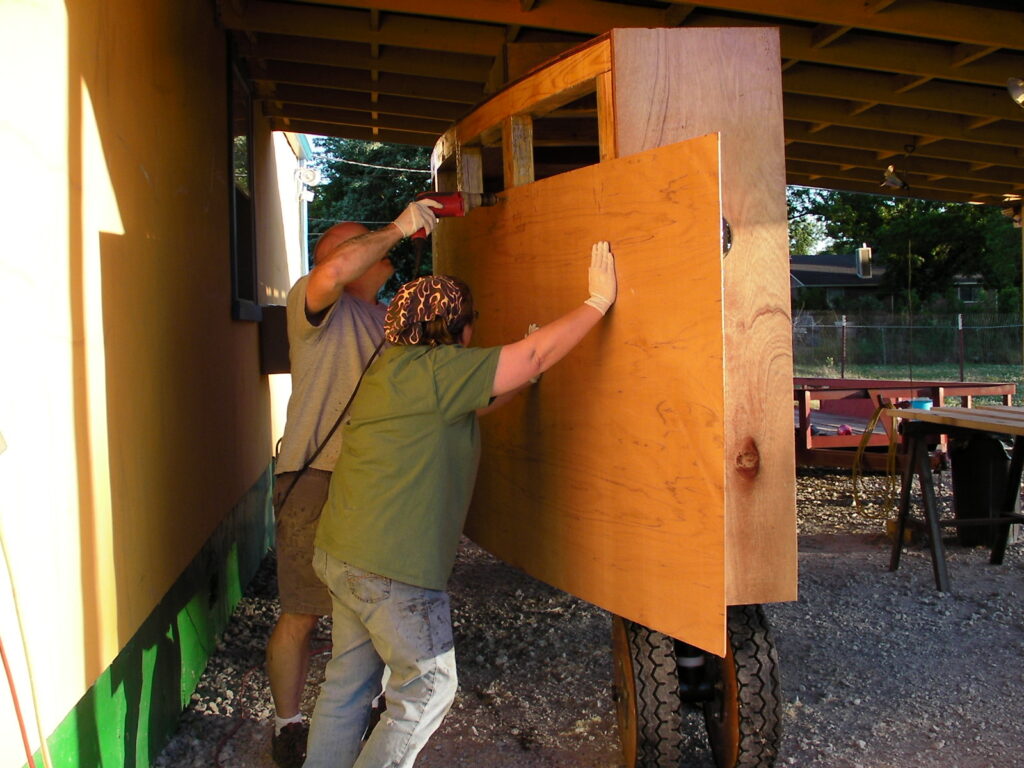
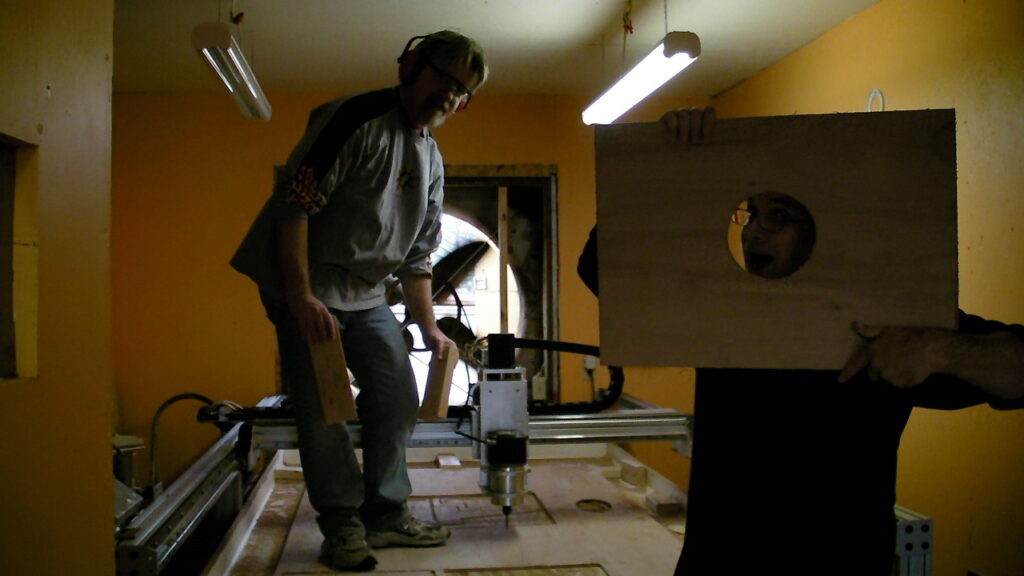